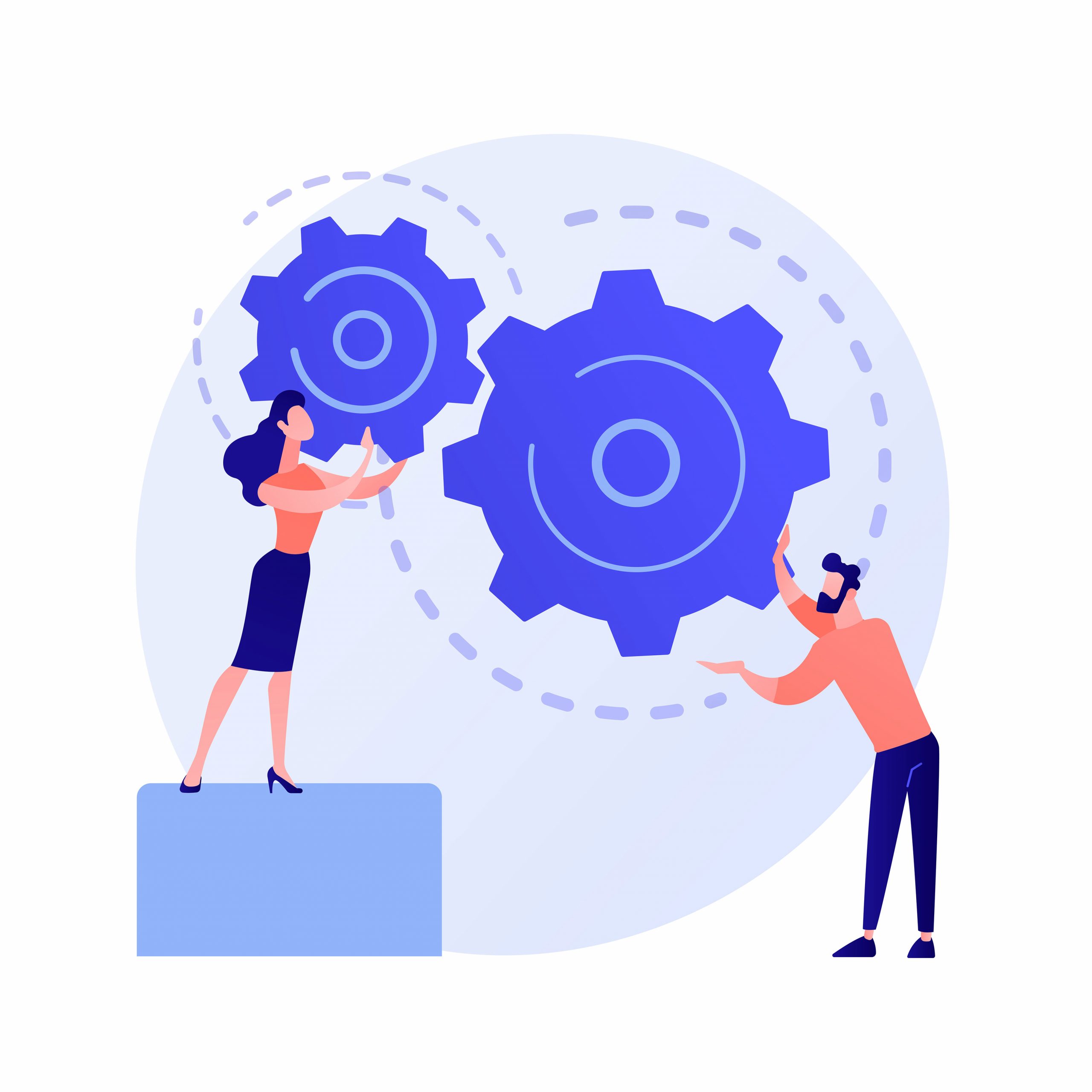
OEE ve FMEA İLİŞKİSİ
Abdullah KARACA
Karacadan Danışmanlık / Yönetim Danışmanı
abdullah.karaca@karacadan.com.tr
www.karacadanismanlik.com.tr
Ocak 2022
Üretim ve hizmet sektörü içerisinde altı ana neden (İş Gücü, Makine, Malzeme, Ölçüm, Metot ve Çevre Şartları) altında detaylandırılabilecek şekilde hata yapma olasılığı vardır. Bazen bu hatalar yüksek oranlarda meydana gelmiş ya da geleceği öngörülmüş olsa da bazen hatalar çok düşük olasılıklarda meydana gelmekte ya da geleceği öngörülmektedir. Hata türlerinin (Özellikle P-FMEA), OEE (Overall Equipment Effectiveness / Toplam Ekipman Verimliliği) arasında oldukça yüksek bir etkileşim olduğu görülmektedir.
OEE hesaplamalarında baz alınan temel kavramlar “Performans”, “Kullanılabilirlik” ve “Kalite” şeklindedir. Teorik olarak OEE bu üç kavramın çarpımı ile oluşmaktadır. Formülü Kullanılabilirlik% x Performans% x Kalite% = OEE% şeklindedir. Kavramların alt detaylarını etkileyen faktörler çok fazla olmakla birlikte bazıları aşağıda örnek olarak verilmiştir.
- Performans = Cycle Time (Çevrim Süresi), Takt Time (Üretim Hızı) ve Machine Proficiency (Makine Yeterliliği) vb.
- Kullanılabilirlik = Planlı Duruşlar (Çay Molaları, Öğle Yemeği, Eğitim vb.), Plansız Duruşlar (Makine Arızaları, İş Kazaları, Elektrik Kesintisi vb.) vb.
- Kalite = FMEA (Failure Mode Effect Analysis / Hata Türleri ve Etkileri Analizi), SPC (Statistical Process Control / İstatistiksel Proses Kontrol), MSA (Measurement System Analysis / Ölçüm Sistemleri Analizi) vb. şeklindedir.
Yalın yönetimde FMEA (Failure Mode Effect Analysis / Hata Türleri ve Etkileri Analizi) üç kategoride sınıflanmıştır. Bunlar D-FMEA (Design Failure Mode Effect Analysis/ Dizayn Hata Türleri ve Etkileri Analizi), P-FMEA (Process Failure Mode Effect Analysis / Proses Hata Türleri ve Etkileri Analiz) ve S-FMEA (System Failure Mode Effect Analysis / Sistem Hata Türleri ve Etkileri Analizi) şeklindedir.
Makalede ele alacağımız P-FMEA aslında ürünlerin veya hizmetlere etki eden hataların OEE üzerine etkisini olan hataların toplamı olarak düşünülebilmektedir. FMEA aslında bir nevi risk analizi olması nedeni ile hesaplama yöntemi “Olasılık” x “Şiddet” x “Sıklık” şeklindedir ve bir puan ortaya çıkmaktadır. Örneğin: Boya kalkma hatası için olasılığımız 2 puan x şiddetimiz / etkimiz 2 puan x sıklığımız 2 puan olduğunu varsayalım, burada bizim P-FMEA puanımız 8 puan şeklindedir. Burada iyileştirme yaparak değiştirebileceğimiz sadece olasılık ve sıklıktır. Şiddet aynı kalacaktır. Baktığımızda ise her hata ürüne veya hizmete aynı şiddette/etkide bulunmaktadır ve bir ürün veya hizmet üzerinde birden fazla hata olabilir bu ise OEE hesabında sapmalara neden olacaktır. Özellikle proje bazlı ve az miktarda ürün üreten (özel makine parçaları vb.) firmalarda sapmalar daha da fazla olmaktadır. Bununla ilgili örnek aşağıdaki gibidir.
Üretim esnasında sadece bir adet üretilecek olan bir ürün için birden fazla hata oluşmuş olabilir.
- Hata-1: Boyanmamış Alan (Basit bir rötuş yapılarak çözülebilir) Düşük Etki
- Hata-2: Delik Eksik (Delik delinerek çözülebilir) Orta Etki
- Hata-3: Ölçülerde Düşüklük (Ürün kurtarılamaz hurdaya ayrılır) Yüksek Etki
Projesis ile her hata modu için ayrı ayrı % değer ya da puan verilerek, OEE hesaplamasında kalite parametresinden kaynaklı sapmanın önüne geçebilmektedir. Örnek aşağıdaki gibidir.
Üretim Adedi: 1 adet
Hata Adedi: 1 adet =Rework yapılmış.
Kalite: -%100
Kullanılabilirlik: %70
Performans: %70
OEE%=-100% (Kalite) x 70% (Kullanılabilirlik) x 70% (Performans) = -49% (Normal Hesap)
Hata yüzdesi önem düzeyine göre 20% aldığımızı varsayalım.
OEE%=(100%-20%) x 70% x70% = 39,20% (FMEA ile hesap)
Sonuç olarak FMEA ile OEE arasında kalite kavramında hata kaynaklı bir bağlantı olup, OEE hesabına direkt olarak etkide bulunmaktadır. Hata modları önem sırasına göre % olarak belirlenir ya da puanlanır ise, OEE hesaplamalarında daha doğru bir yaklaşım olacaktır. Projesis ile bu hesaplamalar ve veri kayıtları oldukça kolay hesaplanabilmekte ve kolayca raporlanabilmektedir.
-
Önceki Makale
Veri Odaklı Değil Karar Odaklı Olmak
-
Sonraki Makale
Endüstriyel PC (Bilgisayar) nedir?